How Plasma Technology Boosted The Automotive And Aerospace Industry
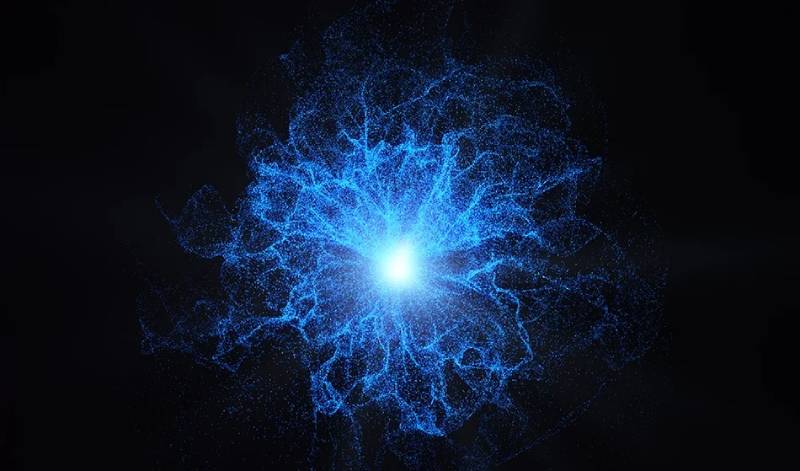
Plasma Technology: Plasma, like solids, liquids, and gas, is a form of matter. Energy is added or removed from a material to change its state. When you apply enough energy to a gas, the molecules become ionized and possess a net positive charge. Sufficient ionization changes the system’s electrical characteristics to the point where it becomes a plasma.
A plasma is made up of positive ions, neutral molecules, negative electrons, UV light, and excited molecules and has a lot of energy. Any or all of these components may interact with surfaces during the plasma treatment process. You may modify the effects of plasma by adjusting the gas combination, the quantity of energy, ambient pressure, and other parameters.
Engineers and researchers typically perform plasma treatment in a vacuum chamber. After removing the air, they introduce a gas, and an electrical field is used to create a plasma. Plasma therapy is often performed at low temperatures, allowing them to treat heat-sensitive materials.
Researchers also carry out plasma treatment technology using atmospheric ‘jet’ plasmas. These plasmas operate at atmospheric pressure and are suited for localized treatment in an in-line manufacturing operation, maybe via automation.
Different industries use Plasma technology, but two of them use it most often and more intricately, the automotive and aerospace industries.
Table of Contents
Characterization of Plasma for Aerospace Technologies
The possibility of active flow management for enhanced aerodynamics of atmospheric aviation is now the focus of plasma studies for the aerospace sector. A plasma actuator is an electrical device that uses low-thermal plasma to modify the airflow fields around a wingspan or fuselage.
This membrane ionizes air molecules and speeds them through an electrical field, which can operate as a vortex generator to increase the vehicle’s aerodynamic qualities while being less mechanically intrusive.
Dielectric barrier discharge (DBD) actuators are being studied for future flight control systems to increase mechanical reactions to air pressures and unfavorable situations.
Although plasma development into this application is still in its early stages, eliminating potentially hefty hydraulic rudder systems might aid in developing progressively lightweight planes for low-pressure flight circumstances.
Non-thermal plasma actuators might be employed for in-flight combustion procedures, allowing for the activation and stability of combustion engines in harsh situations.
According to new plasma research, you might also utilize the non-equilibrium science of a plasma actuator to manage flames created by the peculiar thermodynamic circumstances of orbital and sub-orbital flight.
High-power impulse magnetron sputtering (HPIMS) technologies, which have been employed in advanced material engineering to enhance the surface composition of external air and spacecraft tiles, have also seen increased potential uses due to plasma research.
These high-density films have excellent adhesion and are resistant to strong thermodynamic effects. Pulsed plasma research has improved substrate etching processes, with vast implications in the aerospace sector and beyond.
This emerging plasma research relies on highly circumspect operational control conditions and comprehensive plasma characterizations to ensure that evaluated materials are acceptable for utilization in the aerospace industry.
To ensure excellent purity in HIPIMS implementations, key plasma characteristics must be maintained in development laboratories, ranging from plasma rates and reaction kinetics to manufacturing repeatability.
Application of Plasma Technology in the Aerospace Industry
Plasma-based propulsion technologies are essential applications. The Hall thruster, previously employed for satellite placement and orientation, is the most critical. Large amounts of study are being conducted on this issue to extend this technology’s capability to interplanetary journeys.
Another fascinating aspect of the Hall thruster is the engine and radio transmission disruption. Other plasma-based propulsion systems include laser propulsion and plasma jets.
An additional advancement in plasma technology is the utilization of PECVD. Plasma Enhanced Chemical Vapor Deposition is a cold temperature low – pressure deposition of thin films process that has a strong presence in the semiconductor, automotive, and aerospace industries due to its ability to coat surfaces that would not be capable of withstanding the temperatures of more traditional CVD processes.
Engineers use PECVD in the industrial business in design, architecture, and aerospace disciplines. This procedure is concerned with solar cells and photovoltaics. Because PECVD is a flexible technique, it may spread across larger surfaces, resulting in higher refraction rates on items such as solar panels and eyewear.
Have you ever noticed how the glare on a pair of sunglasses or a solar panel reflects evenly? That is the rate of refraction. Because of the glossy sheen, light bends when it strikes the object’s surface.
The military, automotive, and industrial sectors comprise the microelectronics industry that also uses PECVD. These industries produce computers and other metal parts. The production process culminates with a coating procedure, such as PECVD, before distribution.
Fabricators in this business utilize dielectric materials such as silicon nitride and silicon dioxide. Encasing the PECVD layer creates a corrosion-resistant barrier to the outside climate and humidity.
The Use Of Plasma In The Automobile Industry
Plasma has already established itself in the automobile sector and has become standard in many locations. It is mainly because the quality and process dependability are critical here.
Process rates may be enhanced while maintaining continuous high quality by incorporating plasma technology into the automobile sector. Modern composite materials, such as CFRP (fiber-reinforced plastic), are bonded using plasma. Pre-treatment with plasma can result in long-term durable adhesive bonding.
Application of Plasma Technology in the Automotive Industry
Here are some of the processes that use plasma treatment in the automotive sector:
Surface Treatment
Organic acids were utilized for surface treatment before the introduction of plasma to the automobile sector. When organic acids react with metal surfaces, they produce non-volatile by-products that collect on the metal’s surface, significantly changing its characteristics.
Metal surfaces are now volatile when they react with plasma. Surface treatments enhance a material’s tension without affecting its characteristics.
Surface Cleaning
Some may believe that plasma is merely a surface tension modulator. However, it is much more. Plasma is a highly powerful cleaning agent.
It is capable of cleaning different car parts and removing organic contaminants. Surface cleaning not only enhances the overall grade of the metal but also reduces the chance of corrosion.
Windshields
The margins of the glass panes are covered in ceramic and must be joined with a painted flange of the car’s metal body when they install the windshields.
To get the most exact form of adhesion, ceramic-coated glass surfaces must be treated with chemical primers. The problem with these primers is that they include volatile solvents that are emitted into the environment and potentially into the automobile, which is the last thing you want.
Ideally, you want an ecologically friendly wet-chemical pre-treatment, and plasma therapy has made that feasible.
Conclusion
Plasma technology has multiple applications in the automotive and aerospace industries. It boosted these industries because of the research and advancement in plasma physics.
ALSO READ: Do Ethernet Splitter Slow Down Speed?
ALSO READ: How To Setup Or Enable Wake-On-LAN In Ubuntu