Extending the Limits of USB 3.0 Cable and Connectors
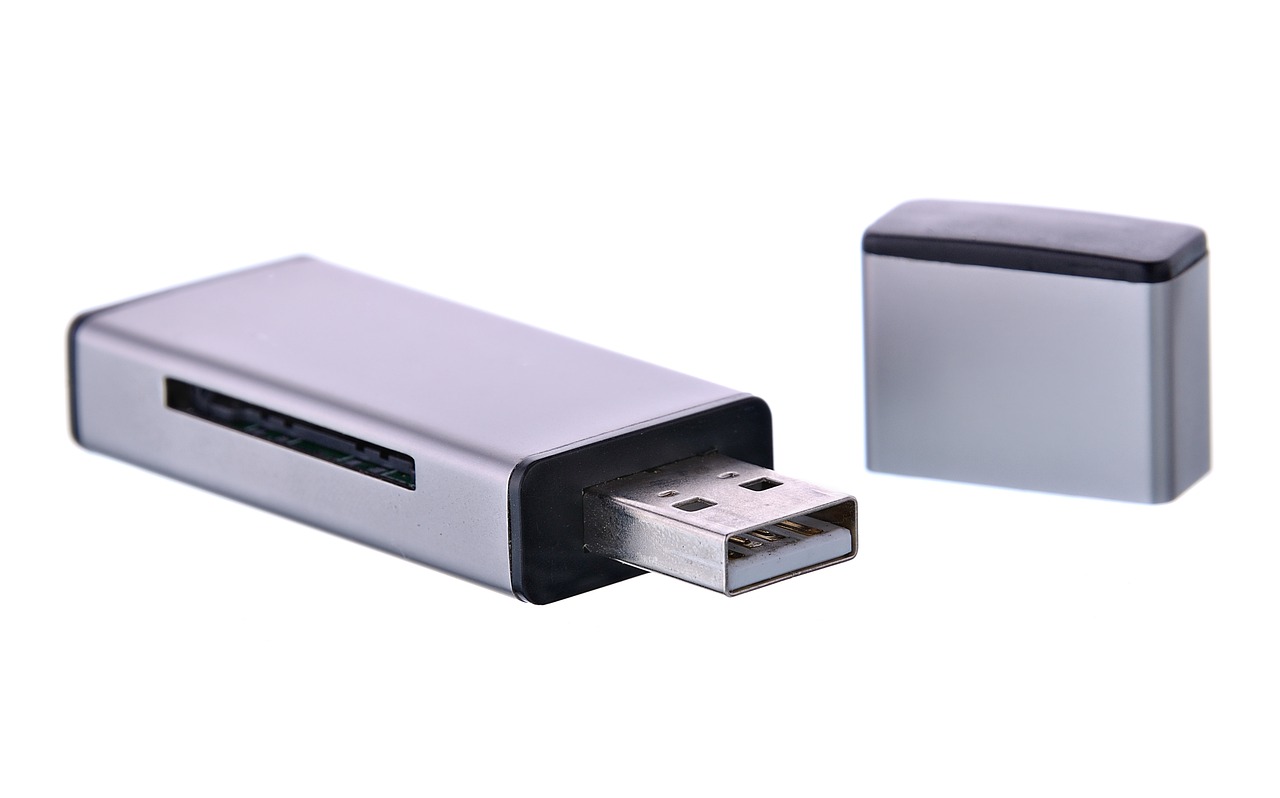
Understanding USB 3.0 cable is essential for connector and cable manufacturers to thrive in this rapidly changing new world.
USB 3.0 is introduced in 2008. There were the first adapters for this new technology, but it took several years for it to become as ubiquitous as it is today. About a decade after its first release, USB 3.0 remains a significant player in today’s electronics.
Table of Contents
Micro DA USB OMNETICS
This technology has been further developed. Cable assemblies have to upgrade accordingly to meet the needs of new complex applications. While the initial USB 3.0 products tended to be well below the 5 Gbps specification, many more unique products try to use this maximum data rate, sometimes with cables up to 5m in length. The combination of higher data rates and longer cable lengths requires maximum performance from the cable assembly.
Mechanical requirements are a question. Although USB develops for the business environment, new industries such as the military and aerospace are trying to implement this technology. It requires a rugged, lightweight connector design, protects against the ingress of dust and water (IP67 / IP68), and can operate successfully under shock and vibration loads while providing over 1000 mating cycles/downgrading.
These challenges require a carefully designed connector and cable. In this article, we’ll introduce USB 3.0 and then outline some of the technical challenges connector and cable manufacturers must consider thriving in this new world.
Technical data and connector types
The USB association released two different conditions: USB 3.1 and USB Type C. These use interchangeably, but these two are separate documents. USB 3.1 mainly defines that electrical supplies for USB 3.1 roles and signals; While the type C requirement primarily defines the connection requirements for the new type C footprint.
The misunderstanding arises from the fact that there are both USB 3.1 and Type C ports. Clarification is needed; there are also TypeA and TypeB connectors for USB 3.1 as well as USB connectors. 2.0 and USB 3.0 using the Type C footprint.
USB 3.0 vs. USB 3.1
Further confusion arose with the USB 3.1 specification when the USB 3.0 descriptor became obsolete. What is often referred to as USB 3.0 is now officially referred to as USB 3.1 Gen 1, and what is commonly understood as USB 3.1 is USB 3.1 Gene. 2. In other words, USB 3.0 no lengthier exists. However, this obsolescence has not prevented most manufacturers from continuing to use the USB 3.0 descriptor. USB 3.0 use to refer to USB 3.1 Gen 1.
Also Read: What is DVI Cable, and What are its Uses?
The advancement of USB 3.0 technology
In the early days of USB 3.0, many cable and connector manufacturers were unable to meet the requirements of USB 3.0. The connector impedance requirement of 90 Ω ± 15 Ω and the recommended offset of 15 ps / m. When Phonetics conducted an informal test on a dozen commercially available USB cable assemblies in 2014, only one of the groups completed the USB 3.0 specification. However, as the products did not reach the limits of technology, performance issues in this area were rarely encountered. The bottom line is that at the start of USB 3.0, even cable assemblies that did not meet USB specifications worked adequate on-site. As a result, there was little motivation to improve their performance.
As technology has evolved, new hardware introduces that uses the 5 Gbps data rate, forcing cable and connector manufacturers to meet all requirements.
Meet connector requirements
Phonetics USB 3.0 ports and cables
USB 3.0 connector ports. The image above shows a good termination. The protective film is pressed firmly against the wires until it is very close to the blue insulation. Conversely, the protective sheet on the lower connector reduces by approximately 1/3 of an inch
The main specification that the connector affects is the differential impedance. The impedance control requires a constant section for critical signals. It is easy to achieve in one cable since the cross-section remains practically constant over the entire cable. It is much more difficult with the connector because the cross-section is constantly changing: signals travel from the wires to the soldering pads and then to the connector pins. Each of these areas has a different cross-section and, therefore, a different impedance. For this reason, the specification using a plug allows a larger impedance range than using a cable (90 Ω ± 15 Ω for the plug versus 90 Ω ± 7 Ω for the cable).
The main area that causes the impedance specification to fail is the signal wires near the pads. In this area, the stop around the twisted pairs removes to connect the wires to the solder pads. The foil uses to change the impedance of the cables. Its removal leads to an increase in the impedance. For this reason, it is essential to minimize the length of the aluminum protector that removes.
Phonetics-USB-Bad, the upper connection shows good termination. The foil protector is held firmly against the wires until it is very close to the blue insulation. Conversely, the protective film on the lower connector is reduced by approx—1/3 inch. The difference between these two ports is likely to be the difference between passing and failing the impedance specification.
Meet cable requirements
The successful design of a USB 3.0 cable must take into account the impedance and intra-pair misalignment of critical pairs.
To match the impedance, you need to control the thickness of the wire insulation, twist the pairs tightly together, and put a shield around each team. Controlling the insulation thickness of the wire and twisting of the groups alone gives a relatively good impedance match, and the foil uses to maintain a tight impedance tolerance throughout the cable.
Minimising intra-pair bias – the time difference between electrical signals within a pair – requires tightly controlled design. If the environment of the two lines of a team is not the same, an offset introduces. It can be due to asymmetries in the wire extrusion, pairs that slightly twists, or slight deviations in the extruded plastic. In short, minimising misalignment requires good cable design and a closely monitored manufacturing process.
It is also essential to consider the length of the cable. To meet specifications, the size of the assembly should keep to a maximum of 2-3 m. Longer lines do not meet the loss requirements. For most applications, this means that the cable will fail the application. Not all apps will fail, however. Omnetics works with customers who can successfully transmit signals over five meters of cable.
Conclusion
In this new time of connector design, mechanical and electrical requirements must consider equally. Find a suitable solution; it is necessary to look at the connector and the cable in the same way. By applying the concepts discussed in this article, a solution is possible that meets the needs of a wide variety of customers.